Biggest-ever agricultural film production line
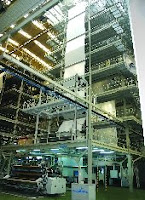
- gravimetric dosing system for each extruder,
- 2 extruders, 150 mm screw diameter,
- 1 extruder, 200 mm screw diameter,
- 3-layer blown film die with internal bubble cooling and 2200 mm die diameter ensuring a high production capacity,
- high-performance air ring KRF 2200,
- film guiding system with 4 ultrasonic sensing arms, collapsing assembly and side gusseting unit,
- 8-ply folding station for C-type folding enabling simple handling of the oversized film widths in greenhouse construction,
- fully automatic short-length winder FAC 4200 with bobbin magazine, adjustable for winding different film lengths and to cope with extremely short reel changing cycles,
- REIcofol automation system for process control, including film measuring station and indication of side gusseting depth.

The new 3-layer blown film line is designed for an extremely high production capacity of 2200 kg/h. Films of a circumference of up to 18,5 metres and thicknesses from 0,080 to 0,200 mm can be produced on this line. The immense total construction height reaches 35 metres. Coextruded 3-layer films are distinguished by specific properties, e.g. weather resistance, permeability to light, air-conditioning effects and high tear resistance. In addition, the consumption of raw materials processed on coextrusion lines is considerably reduced. A great advantage of a coextrusion line over a mono-layer line is that expensive additives can be used in the thin outer layers only. Also, exact matching of materials to requirements is much simpler. Multi-layer films with a durability of up to four years can be very economically produced as a result.
Comments